What cutting tools should be selected before machining the casing?
The shell materials of hard alloy cutting tools are carbon steel, stainless steel, aluminum alloy, titanium alloy, polymer material, etc. Due to the limitations of the material itself, hard alloy cutting tools cannot be used during processing. If hard alloy cutting tools are used, they will scratch the shell and affect the surface smoothness of the shell.
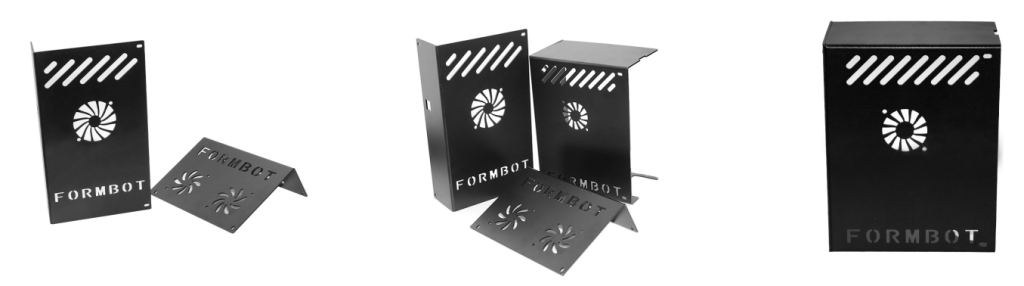
High speed steel cutting tools are suitable for rough machining of shells. High speed steel cutting tools have good wear resistance, sharp cutting edges, and can ensure the surface smoothness of the shell.
Diamond cutting tools are suitable for precision machining of shells, as their high hardness, machining accuracy, and smoothness do not guarantee the surface smoothness requirements of the cut surface during rough machining.
Superhard material tools superhard material tools include cubic boron nitride tools, ceramic tools, cermet tools, etc. these tools are characterized by high hardness, good wear resistance, high machining accuracy and smoothness, but they are expensive. 2、 What are the machining processes for the shell?
Milling is the process of continuously rotating a milling cutter on a plane perpendicular to the grinding wheel to remove the surface of the shell. Two types of milling are commonly used: flat milling and three-dimensional milling. Good appearance and flatness during rough milling. It is easy to control vibration during precision milling. Large machining allowance. Small chip space, easy to crush the blade and uneven cutting thickness. Suitable for linear and circular interpolation movements on flat or inclined surfaces.
Drilling drilling is the process of drilling holes on the shell with a Fried Dough Twists drill. It is difficult to remove chips during drilling and is not suitable for high-precision hole processing. But the size and shape of the hole can be directly obtained. Due to the low cutting resistance during drilling, chip removal is easy and chip breakage is relatively easy, making it suitable for processing small and medium-sized precision holes.
Boring machining is the process of using a boring head to insert in a plane perpendicular to the spindle. It is suitable for machining holes with larger diameters and higher accuracy requirements. During boring, due to the high cutting resistance, chips are not easily discharged, resulting in chip buildup and high cutting temperature, making it unsuitable for high-speed machining.
Planer machining is the process of using a planer to perform reciprocating linear motion on a plane parallel to the grinding wheel to plane the surface of a workpiece. It is suitable for machining vertical and horizontal planes on flat surfaces and inclined surfaces. The planing speed is low, the production efficiency is relatively high, and high accuracy can be achieved.